Who Are We?
About us
ADAPTED Research Group (formerly known as Advanced Process Control Methods Research Group) is part of the Automation Department of the Faculty of Automation and Computer Science and the Energy Transition Research Center (EnTReC) from the Technical University of Cluj-Napoca.
ADAPTED Research Group conducts research in optimal, robust, fractional order control with a broad range of applications, although much of the research is centered around the development and application of advanced control techniques to complex chemical systems.
The main goal of the group is to develop practically relevant control system design and analysis tools. Our research, therefore, includes both fundamental control theory problems and applications of the developed tools to complex, emergent systems.
AREAS OF EXPERTISE
Complex process modelling and simulation:
- Detailed models and simulations of various industrial and medical processes.
Tuning, design and testing of various control solutions including advanced control algorithms such as predictive, fractional or robust control:
- Conceptual design of various control loops from classical PID to advanced control algorithms;
- Control strategy implementation;
- Control optimization.
Particular advanced monitoring, supervising and control methods for non-conventional processes and technologies:
- Conceiving of new, efficient technologies in isotopic and molecular processes;
- Modelling, monitoring and control of biochemical and biomedical processes;
- Improved efficiency based on optimization; process maintenance.
OUR TEAM
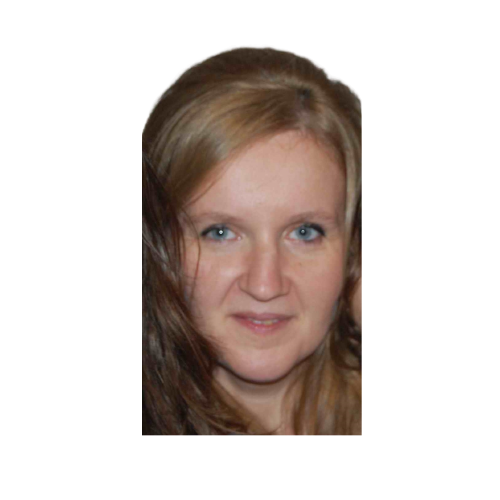
Eva H. DULF
Head of ADAPTED Group. Prof. Habil. Dr. Eng.
- Email:Eva.Dulf@aut.utcluj.ro
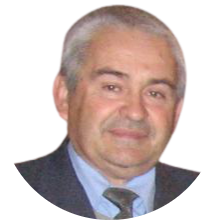
Clement Feștilă
Prof. Dr. Eng.
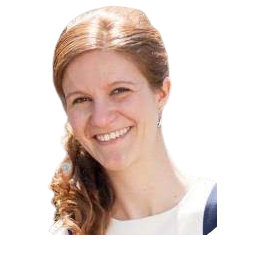
Cristina I. Mureșan
Prof. Dr. Eng.
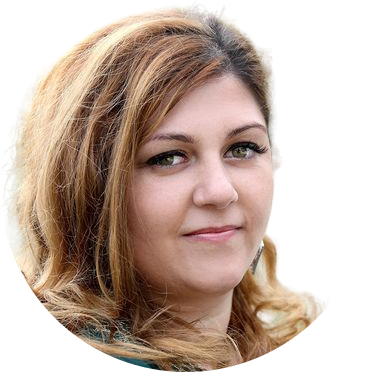
Roxana Rusu-Both
Assoc. Prof. Dr. Eng.
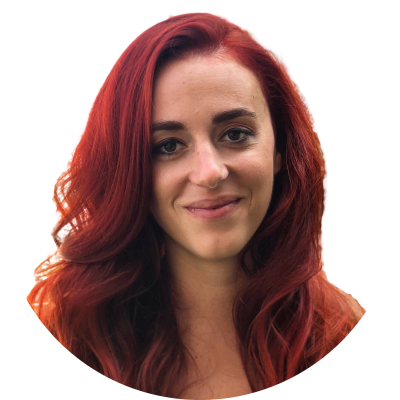
Ioana Nașcu
Assoc. Prof. Dr. Eng.
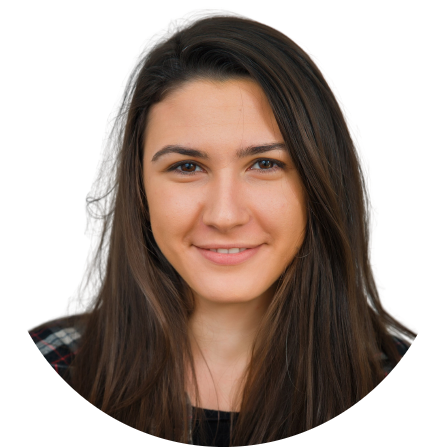
Isabela Bîrs
Lect. Dr. Eng.
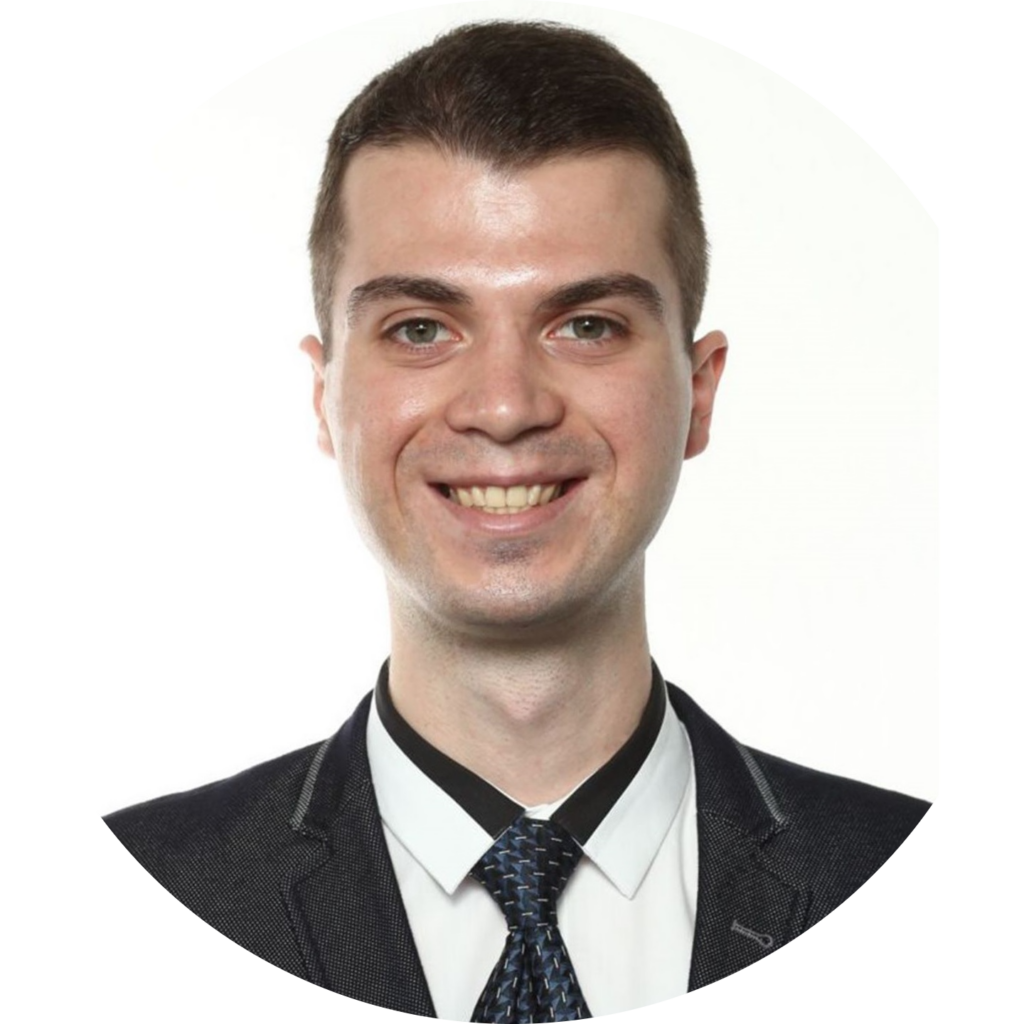
Alexandru G. Berciu
As. Drd. Eng.
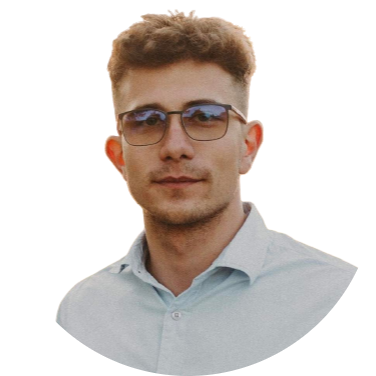
Marcian MIHAI
As. Drd. Eng.
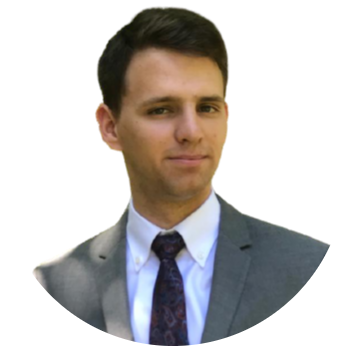
Daniel Timiș
Drd. Eng.
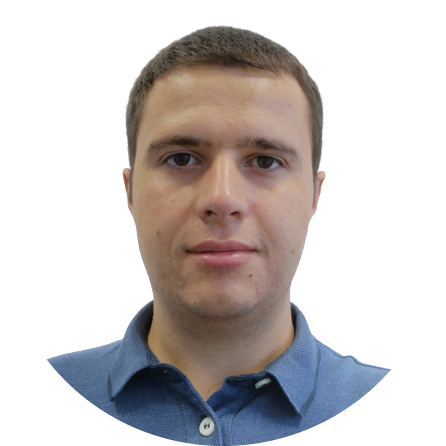
Toader Serețan
Drd. Eng.
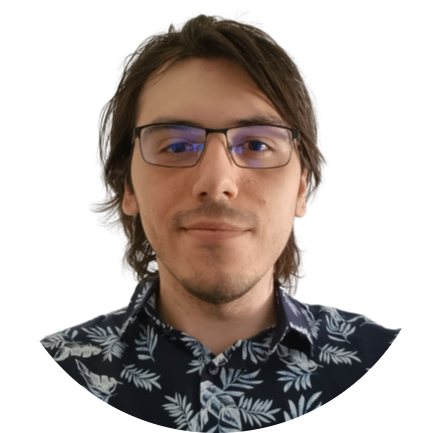
Alex Ede Danku
Drd. Eng.
- Email:Alex.Danku@aut.utcluj.ro
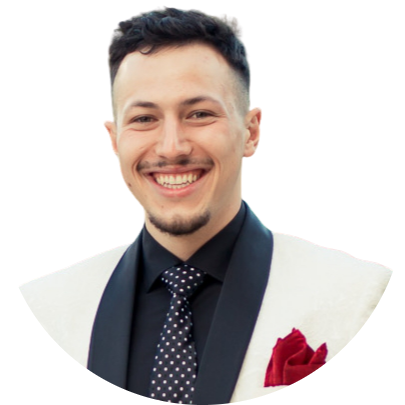
Andrei Tulbure
Drd. Eng.
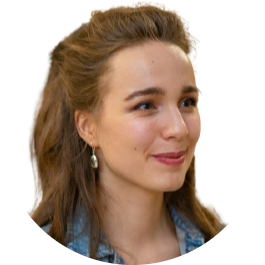
Noemi Lorenzovici
Drd. Eng.
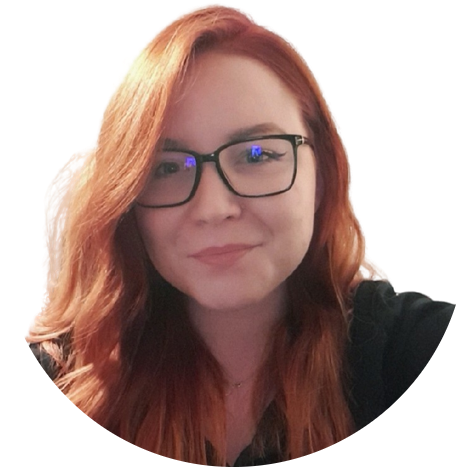
Elisabeta KOZMA
Drd. Eng.
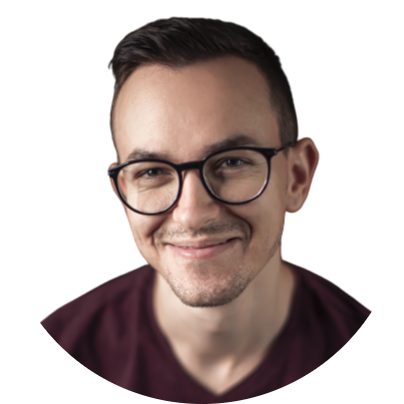
Erwin T. Hegedüs
Drd. Eng.
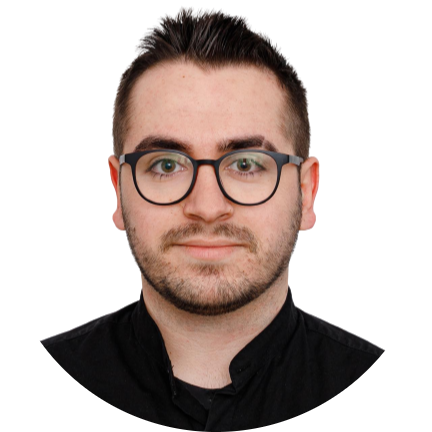
Paul Pintea
Eng.
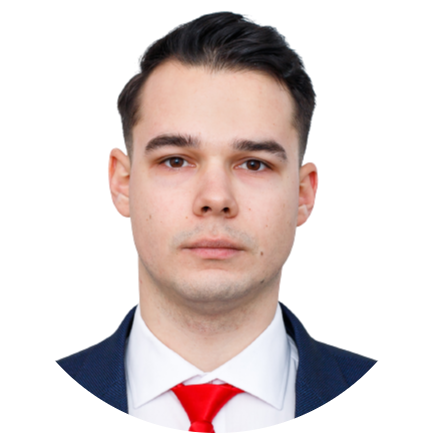
Ovidiu Ceoca
Eng.
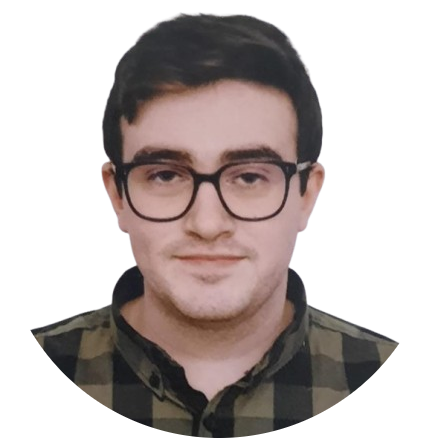
Sebastian Mănase
Eng.
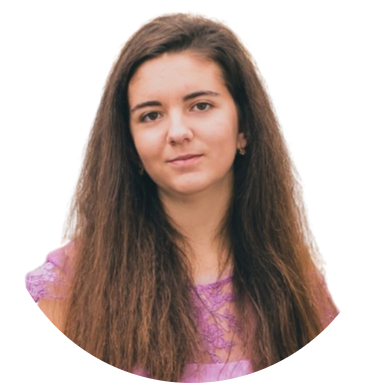
Nicoleta Bădău
Eng.
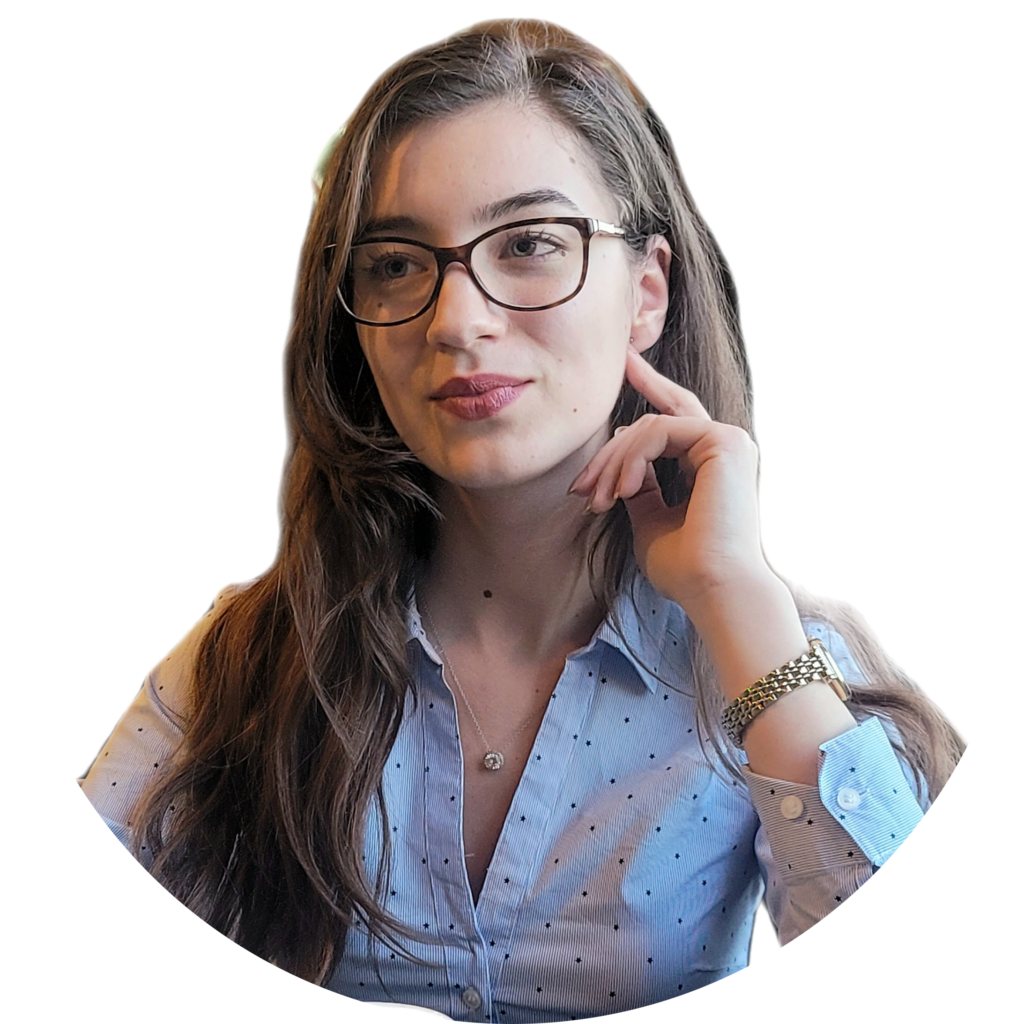
Loredana Buliga
Eng.
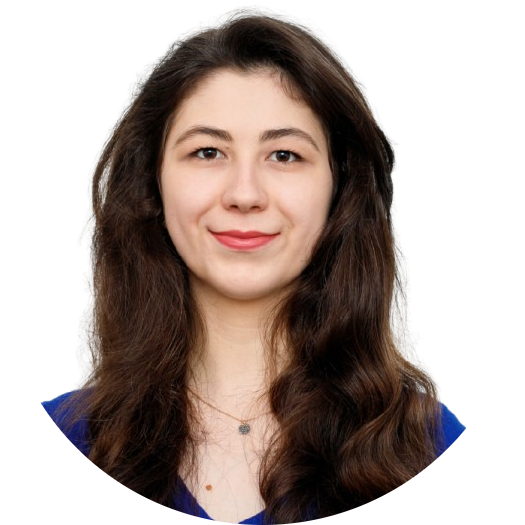
Teodora Popescu
Eng.
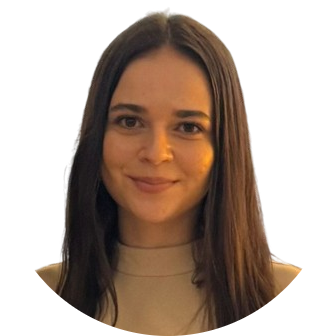
Diana-Mihaela Dobocan
Eng.
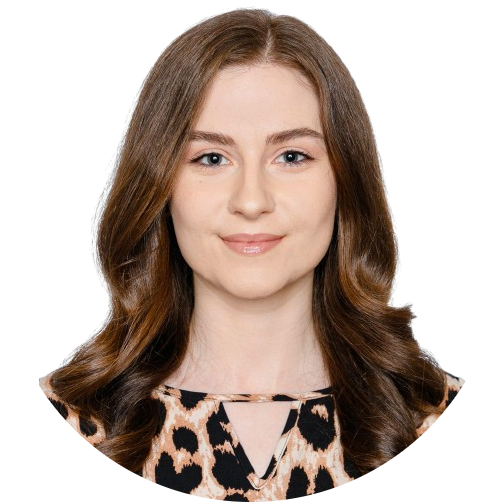
Delia-Ramona Santa
Eng.
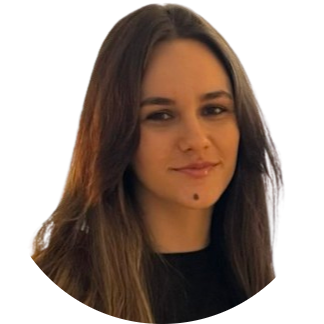
Andreea-Roxana Todea
Eng.
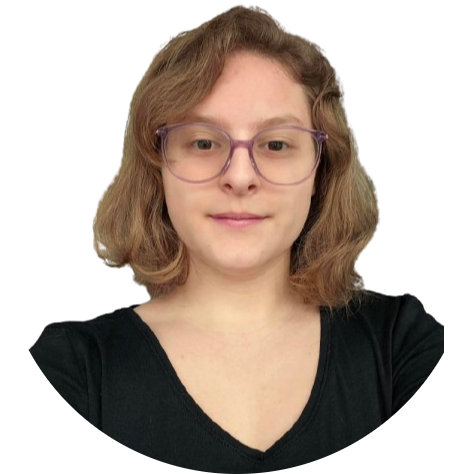
Ada-Maria Tudor
Eng.
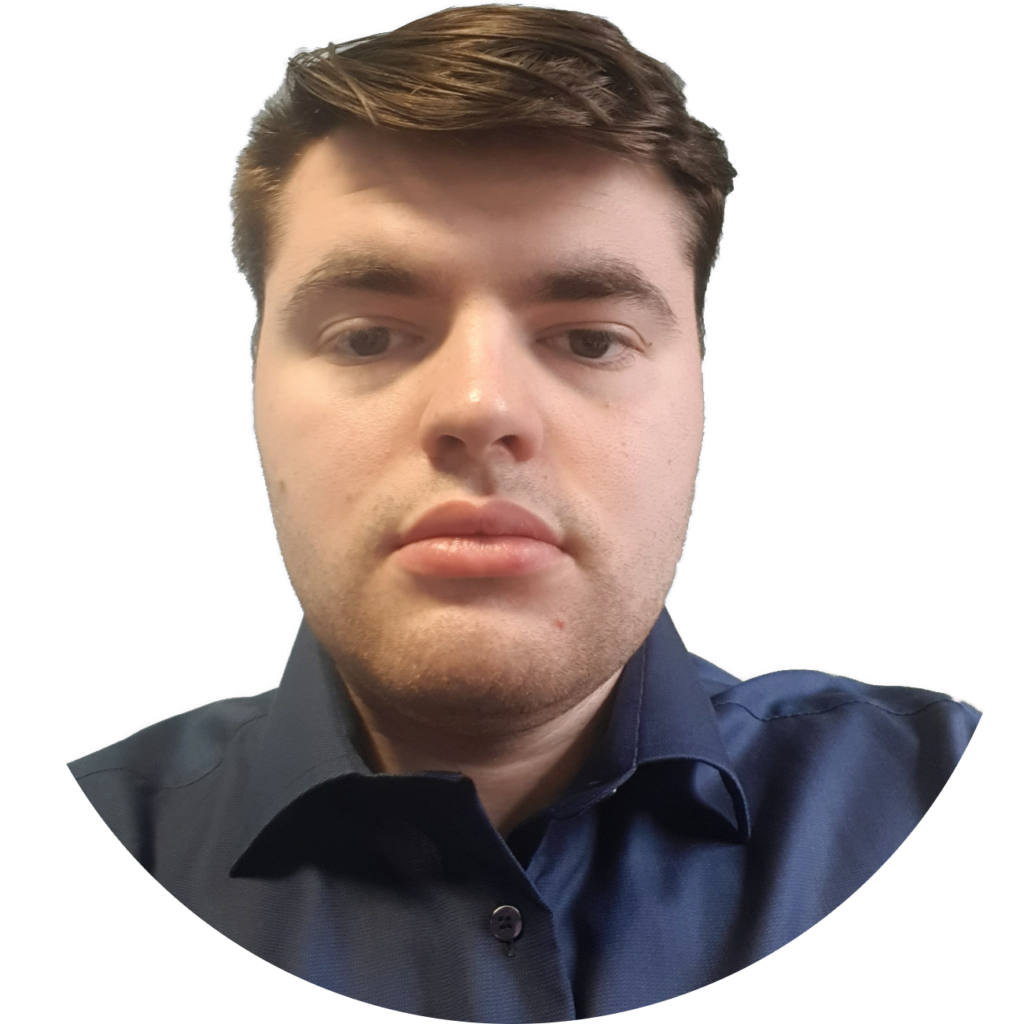
Alin-Ciprian Malița
Eng.
Research Services
Team members:
- Cristina MUREȘAN;
- Eva-Henrietta DULF;
- Toader SERETAN;
- Ioana NAȘCU.
Team members:
- Cristina MUREȘAN;
- Eva-Henrietta DULF;
- Daniel TIMIȘ;
- Alex DANKU;
- Isabela BÎRS;
- Alexandru-George BERCIU.
Team member:
- Marius GRETINGER.
Team members:
- Roxana BOTH-RUSU;
- Clement FEȘTILĂ.
Team members:
- Cristina MUREȘAN;
- Eva-Henrietta DULF;
- Alex DANKU.
Team member:
- Andrei - Alexandru TULBURE.
Team member:
- Andrei KOVARI.
Team members:
- Cristina MUREȘAN;
- Eva-Henrietta DULF;
- Roxana BOTH-RUSU;
- Alex DANKU;
- Andrei KOVARI;
- Noemi LORENZOVICI;
- Alexandru-George BERCIU.
Team members:
- Cristina MUREȘAN;
- Ioana NAȘCU.
Team member:
- Ioana NAȘCU.
Team members:
- Eva-Henrietta DULF;
- Alexandru-George BERCIU.
OUR OFFER
- Identifying fundamental principles and methodologies that enable systems to exhibit intelligent, goal-oriented behaviour, and developing innovative instruments to monitor, manipulate, and control systems;
- Tuning, design and testing of various control solutions using advanced control algorithms, such as predictive, fractional or robust control;
- Modelling biochemical and biomedical processes.
- Consulting in simulation, design, implementation and maintenance of control systems for multiple industrial field;
- Consulting in structural and nonlinear modelling of complex processes;
- Consulting in process management using different simulation environment.
- Complex process modelling and simulation;
- Tuning, design and testing of various control solutions using advanced control algorithms, such as predictive, fractional or robust control.
Research Equipment
Description: SIEMENS SIMATIC S7-1200 PLC (CPU 1215C PN): – 14DI/ 10DO/ 2AI. – SIEMENS SIMATIC S7-1200 AI/AO MODULE: – 4AI/ 2AO. – SIEMENS SIMATIC S7-1200 AO MODULE: – 1AO. – SIEMENS SIMATIC S7-1200 POWER MODULE: – 120/230 V AC, 24 V DC, 2.5 A.
Production Year: 2016.
Description: The PROSIM system is an advanced process simulator that can be used for learning the programming principles of PLC equipment; A number of 33 masks simulating a diverse set of processes, grouped by degrees of difficulty, make the PROSIM system a valuable teaching tool. All inputs and outputs have been designed according to industry standards, i.e. 24V for digital and 0-10V for analogue sizes, bringing more realism to the simulated processes and allowing to work on real industrial equipment.
Production Year: 2016.
Description: ACS-1000, covered with many technical disciplines, explicates the central significance of Analog Control System. It applies particularly in mechanical and electrical engineering, and as well in production and process techonology. In the automation field, important optimization tasks would be quite impossible to be accomplished without closed-loop control technology. The equipment can be used in 35 experiments: from Laplace transform to simulations of PID control algorithms designed by various methods, but also to analyse state feedback.
Production Year:
Description: NI PXI systems provide high-performance modular instruments and other I/O modules that feature specialized synchronization and key software features for test and measurement applications from device validation to automated production test. NI is the PXI industry leader, with the broadest array of best-in-class products and services on the market.
Production Year:
Description: Students can use myRIO to explore fundamental topics in engineering.
Production Year:
Description: Two-Wheeled Unstable Transporter is an example of quite a complex control system. It is obliged simultaneously meet two control algorithms. The first one is a master regulator. It is responsible to maintain the transporter in the upper unstable equilibrium point. The second one has to follow the predetermined trajectory of the vehicle. Linear quadratic regulators in various forms serve in both control algorithms.
Production Year: 2018.
Description: The Multitank System comprises a number of separate tanks fitted with drain valves. Two of the tanks have varying cross sections. These introduce nonlinearities into the system. A variable speed pump is used to fill the upper tank. The liquid outflows the tanks due to gravity. The tank valves act as flow resistors. The area ratio of the valves is controlled and is used to vary the outflow characteristics. Each tank is equipped with a level sensor.
The general objective of the control is to reach and stabilize the level in the tanks by an adjustment of the pump operation or/and valves settings. This control problem can be solved by a number of level control strategies ranging from PID to adaptive and fuzzy logic.
Production Year: 2017.
Description: Antilock Braking Systems are designed to optimize braking effectiveness while maintaining car controllability. The ABS model is driven by a flat DC motor steered from a PC.
There are two encoders measuring the rotational angles of two wheels. At the beginning of an experiment the wheel simulating the relative road motion is accelerated to an assumed threshold velocity. The car wheel accelerates following the rotational motion of the imitating road wheel. If the threshold velocity is achieved a braking procedure starts. If the car wheel becomes motionless it means that it remains in slip motion (the car velocity is not equal to zero) or it is absolutely stopped. The less the slip the better is car control.
Production Year: 2017.
Description: Two Rotor Aerodynamical System (TRAS) is a set-up designed for control experiments. In certain aspects its behavior resembles that of a helicopter. From the control point of view it exemplifies a high order nonlinear system with significant cross-couplings.
Production Year: 2018.
Description: Modular Servo is designed especially for the study and verification of basic and advanced control methods in practice. It includes demonstration of typical variable factors such as friction, damping and inertia as well as a number of position/ speed control methods ranging from PID to LQ and time optimal control.
Production Year: 2017.
Description: The NI Educational Laboratory Virtual Instrumentation Suite (NI ELVIS) is a modular engineering educational laboratory device. Includes an oscilloscope, digital multimeter, function generator, variable power supply, Bode analyzer, and other common lab instruments. You can connect a PC to the NI ELVIS using USB and build circuits on its detachable protoboard.
Production Year: 2018.
Description: The QNET Myoelectric trainer is an exciting way to study biomedical engineering. Students can learn how to control a servo from the contraction of muscles.
Production Year: 2018.
Description: The Quanser QNET VTOL Board 2.0 for NI ELVIS has been developed for education to facilitate hands-on, active learning of flight dynamics with a 1 degree of freedom (DOF) helicopter that introduces kinematics, vertical take-off, PI, and PID control. The application board provides a variable-speed fan mounted on a cantilever arm with a high-resolution optical encoder for position measurement. Using the Quanser QNET VTOL Board 2.0 for NI ELVIS II/II+, you can provide experiential-based learning in mechanical, mechatronics, and aerospace engineering.
Production Year: 2018.
Description: The Quanser QBot 2e is an innovative open-architecture autonomous ground robot, equipped with built-in sensors, and a vision system. Accompanied by extensive courseware, the QBot 2e is ideally suited for teaching undergraduate and advanced robotics and mechatronics courses, surpassing capabilities of hobby-level robotic platforms. The open-architecture control structure allows users to add other off-the-shelf sensors and customize the QBot 2e for their research needs.
Production Year: 2018.
Description: mBot Ranger provides 3 models, Robot Tank, Self-balancing Robot, Racing car in one set. After finishing building the robot, students can use the MAKEBLOCK app to control the robot and use Scratch or Arduino C language to program it for further learning.
Production Year: 2017.
Description: • INTERCONNECTED GRADUATED TANKS;
• COLLECTOR TANK;
• SOLENOID VALVES;
• CONTROL ELECTRONICS FOR SOLENOID CONTROL VALVES;
• SIEMENS SINAMICS G110 FREQUENCY INVERTER;
• SIEMENS SINAMICS G110 BASIC OPERATOR PANEL (BOP);
• SIEMENS SITRANS PRESSURE TRANSDUCERS;
• SIEMENS SITRANS LEVEL TRANSDUCERS;
• FLOW TRANSDUCERS;
• LEVEL SENSORS;
• PUMP;
• CONSTANT FLOW AUXILIARY PUMPS;
• POWER SUPPLY 24 V DC, 3A.
Production Year: 2016.
Model: Creality Sermoon V1.
Production Year: 2018.
Description: The aluminum beam itself is 250mm long, 20mm wide and 1mm thick and has one fixed end and another one free to vibrate/oscillate. The flexible beam is equipped with strain gauge type sensors and actuators (P-878 DuraAct Power Patch Transducers from Physik Instrumente). The control unit is enclosed in a chassis (E501.00) from Physik Instrumente, equipped with a power amplifier (E503.00) and the signal processing module (E509.X3). The programmable automatic controller includes a real time controller (NI 9014) from National Instruments, a chassis with FPGA (NI 9103), two extension modules with analog input lines (NI 9230) for reading data from the sensors (PR) on the beam and analog output lines (NI 9263) for sending the control signal to the piezoelectric patches (PZT).
Production Year: 2018.
Description: The setup consists in a small scale submersible (equipped with a motor and a propeller blade, a wifi module with microcontroller unit and an accelerometer, etc.) and a system of tubes simulating the circulatory system (equipped with a flow meter, pump and control unit).
Production Year: 2018.
Description: The process control learning system (BPCLS) covers industrial-standard applications for open-loop and closed-loop control regarding level, flow, pressure, and temperature processes. It leverages the basic IO and programming PLC capabilities with the Siemens S7-1200 automation configuration and the basic graphic assets of the Siemens HMI KTP700. The main benefits of BPCLS consist of an enhanced learning experience for process control and speed-up of the training in a safe, controlled environment with minimal risk. The user can acquire hands-on experience with calibration, operation, and troubleshooting of the industrial equipment (pumps, flow-level-pressure-temperature transducers, inverter).
Production Year:
Description: The Ultracortex is an open-source, 3D-printable headset designed to work with the OpenBCI system. It is a tool for recording research-grade brain activity (EEG).
Production Year: